Detailed PCBA production process (including SMT process), come in and see!
01."SMT Process Flow"
Reflow welding refers to a soft brazing process that realizes the mechanical and electrical connection between the welding end of the surface-assembled component or the pin and the PCB pad by melting the solder paste pre-printed on the PCB pad. The process flow is: printing solder paste - patch - reflow welding, as shown in the figure below.
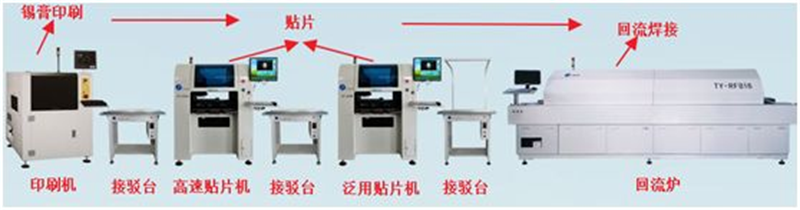
1. Solder paste printing
The purpose is to apply an appropriate amount of solder paste evenly on the solder pad of the PCB to ensure that the patch components and the corresponding solder pad of the PCB are reflow welded to achieve a good electrical connection and have sufficient mechanical strength. How to ensure that the solder paste is evenly applied to each pad? We need to make steel mesh. The solder paste is evenly coated on each solder pad under the action of a scraper through the corresponding holes in the steel mesh. Examples of steel mesh diagram are shown in the following figure.
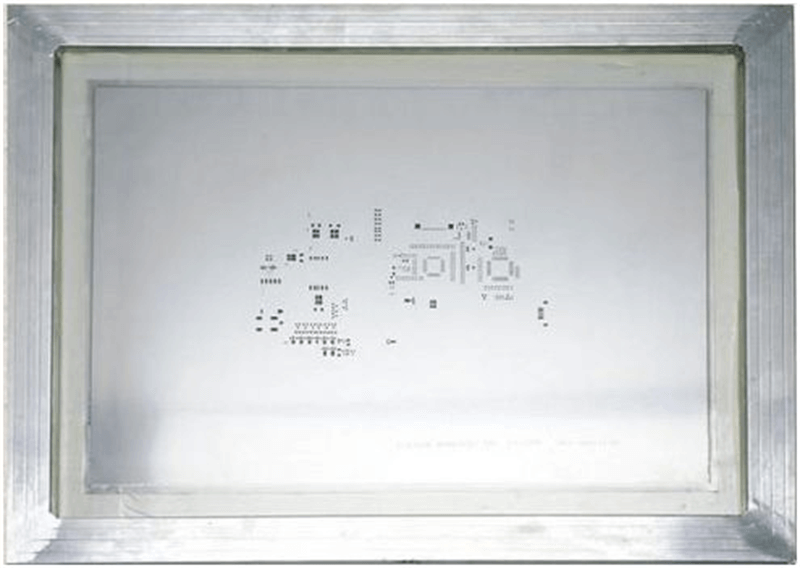
Solder paste printing diagram is shown in the following figure.
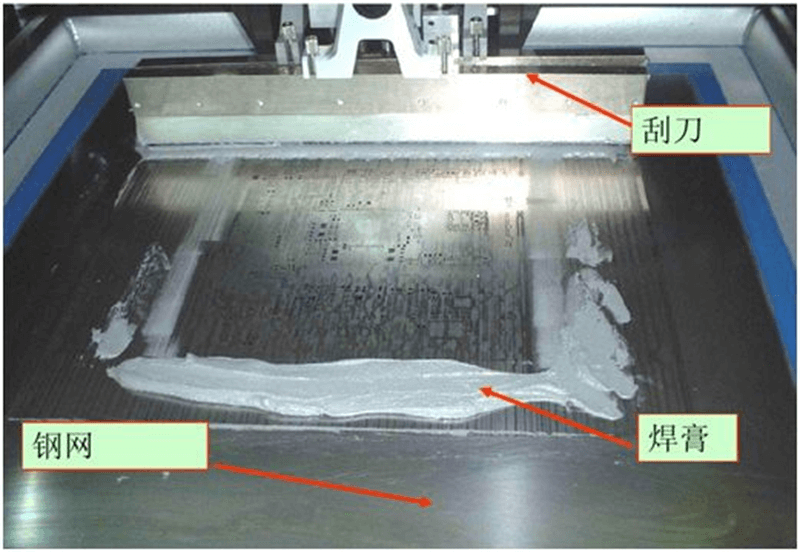
The printed solder paste PCB is shown in the following figure.
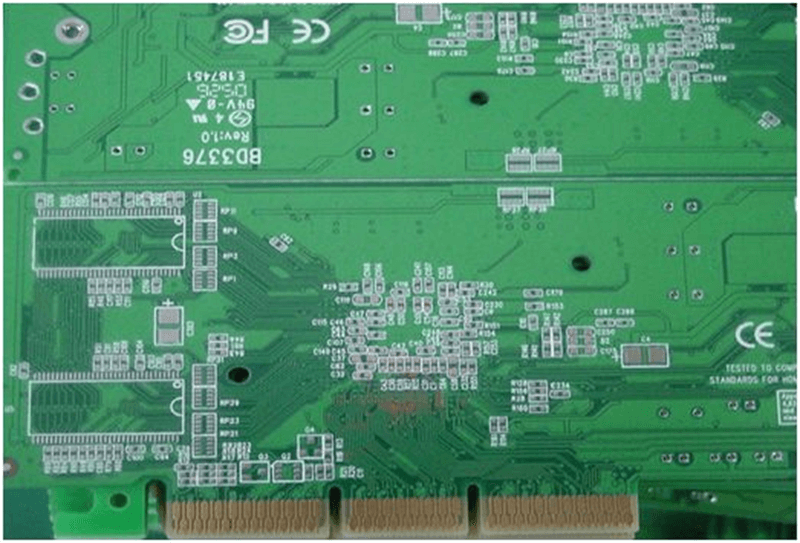
2. Patch
This process is to use the mounting machine to accurately mount the chip components to the corresponding position on the PCB surface of the printed solder paste or patch glue.
SMT machines can be divided into two types according to their functions:
A high-speed machine: suitable for mounting a large number of small components: such as capacitors, resistors, etc., can also mount some IC components, but the accuracy is limited.
B Universal machine: suitable for mounting the opposite sex or high precision components: such as QFP, BGA, SOT, SOP, PLCC and so on.
The equipment diagram of the SMT machine is shown in the following figure.
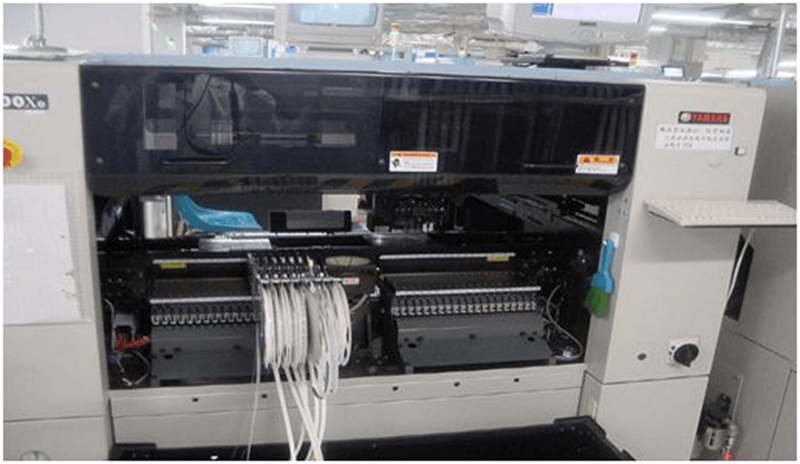
The PCB after the patch is shown in the following figure.
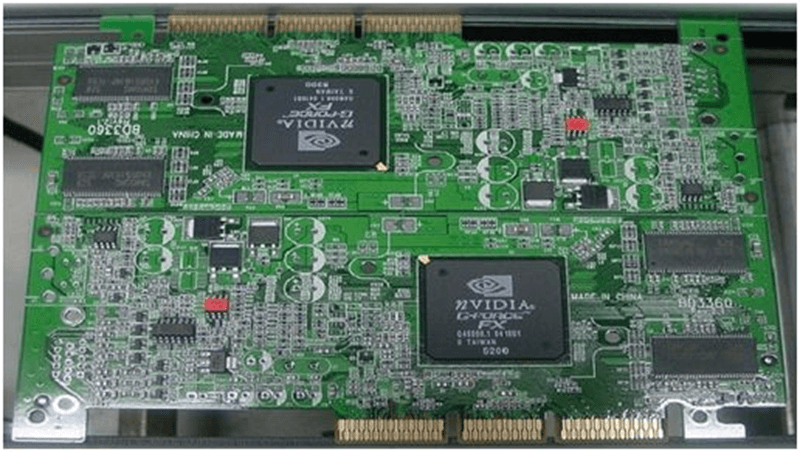
3. Reflow welding
Reflow Soldring is a literal translation of the English Reflow soldring, which is a mechanical and electrical connection between the surface assembly components and the PCB solder pad by melting the solder paste on the circuit board solder pad, forming an electrical circuit.
Reflow welding is a key process in SMT production, and reasonable temperature curve setting is the key to guarantee the quality of reflow welding. Improper temperature curves will cause PCB welding defects such as incomplete welding, virtual welding, component warping, and excessive solder balls, which will affect product quality.
The equipment diagram of reflow welding furnace is shown in the following figure.
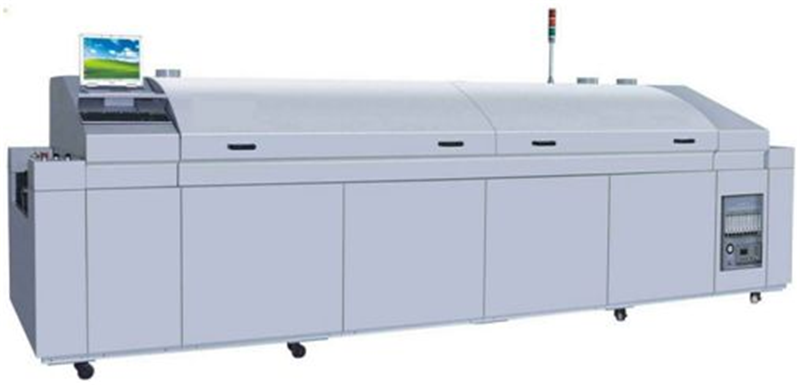
After reflow furnace, the PCB completed by reflow welding is shown in the figure below.